金属製品をカスタマイズする場合、適切な加工方法を選択することは、製品の品質、コスト、納期にとって非常に重要です。金属をカスタマイズするには、さまざまな一般的な方法があります。一般的に使用されるメタルのカスタマイズ方法をいくつか紹介します。
1.CNC加工:
CNC (Computer Numerical Control) 加工は、コンピュータ制御の工作機械を使用して金属を精密に切断および加工する方法です。CNC 加工では、事前にプログラムされた命令を利用することで、複雑な形状や精密な要件を持つ製品に適した金属部品の高精度かつ効率的なカスタマイズが可能になります。
利点:
高い精度と精度
幅広い適合材質
複雑な形状や複雑なデザインに適しています
小規模生産でも大規模生産でも効率的
短所:
初期設定コストが高い
複雑なデザインの場合は生産時間が長くなる
サブトラクティブマニュファクチャリング(材料除去)に限定
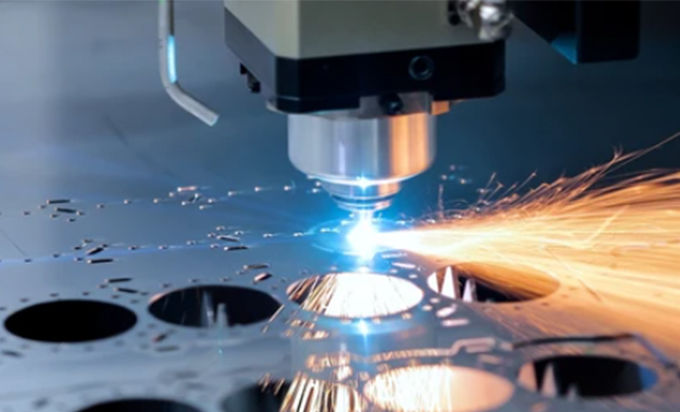
2.フライス加工と旋削:
フライス加工と旋削では、加工装置の工具を使用してワークピースから金属材料を切り取り、カスタマイズされた形状とサイズを実現します。フライス加工は平面や複雑な表面の加工に適しており、旋削加工は円筒状のワークピースに使用されます。
利点:
精密かつ正確な加工
さまざまな形状やサイズに対応できる多用途性
試作と大規模生産の両方に適しています
幅広い適合材質
短所:
複雑なデザインの加工時間の延長
設備費やメンテナンス費が高くなる
旋削加工における回転または対称部品に限定
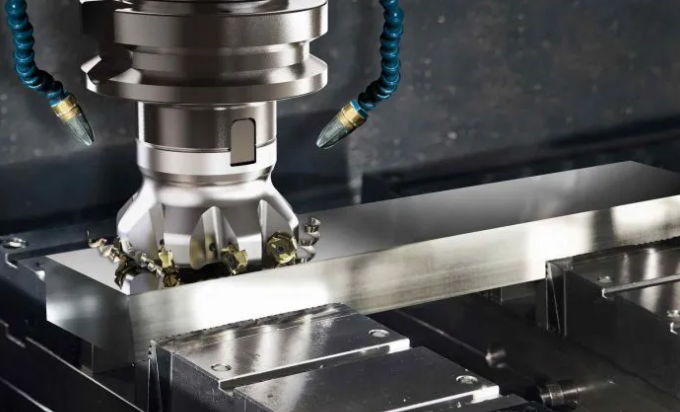
3.3D プリント:
3D プリント技術を使用すると、材料を層ごとに堆積することで金属部品をカスタマイズできます。金属粉末を溶かしたり固めたりすることで、複雑な形状の金属部品を直接印刷することができ、スピード、柔軟性、カスタマイズ性などのメリットが得られます。
利点:
高度にカスタマイズ可能な複雑なデザイン
迅速なプロトタイピングとリードタイムの短縮
従来の方法と比較して材料の無駄が少ない
少量生産に最適
短所:
従来の方法と比較して材料の選択肢が限られている
一部の従来の方法に比べて強度と耐久性が低い
大型部品の生産速度が遅くなる
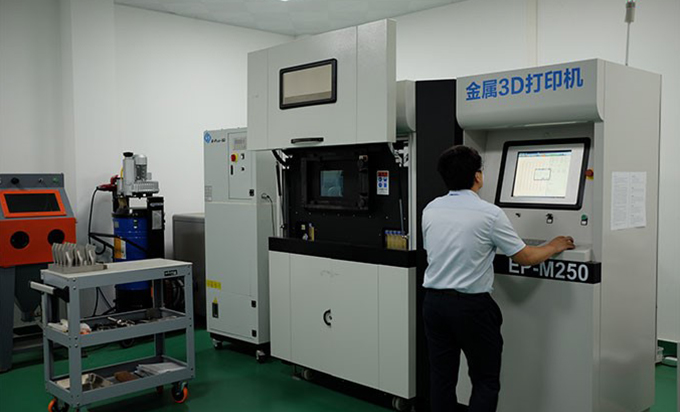
4.レーザー切断:
レーザー切断は、高エネルギーのレーザー光線を使用して金属材料を溶解、蒸発、または燃焼させて切断する方法です。レーザー切断には、高精度、高速、非接触、変形の最小化などの利点があり、幅広い金属部品や構造のカスタマイズに適しています。
利点:
高精度で細かいディテールまで
速い切断速度
非接触プロセスで材料の歪みを最小限に抑える
さまざまな金属と厚さに適しています
短所:
2D 切断プロファイルに限定される
設備費やメンテナンス費が高くなる
エッジを滑らかにするには追加の後処理が必要な場合があります
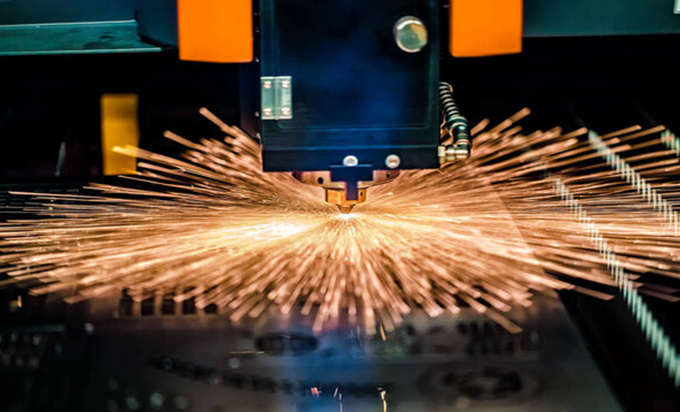
5.スタンピングそして形成:
スタンピングおよびフォーミングでは、金属材料に圧力を加えて目的の形状に成形します。コールド スタンピングまたはホット スタンピング プロセスを使用すると、複雑な形状と高精度のカスタム金属部品やコンポーネントを実現できます。
利点:
大量生産の高速生産
繰り返しの設計にコスト効果が高い
複雑な形状や厳しい公差に適しています
強化された材料強度と耐久性
短所:
初期工具コストが高い
特定の形状とサイズに限定される
プロトタイプや少量生産には理想的ではありません
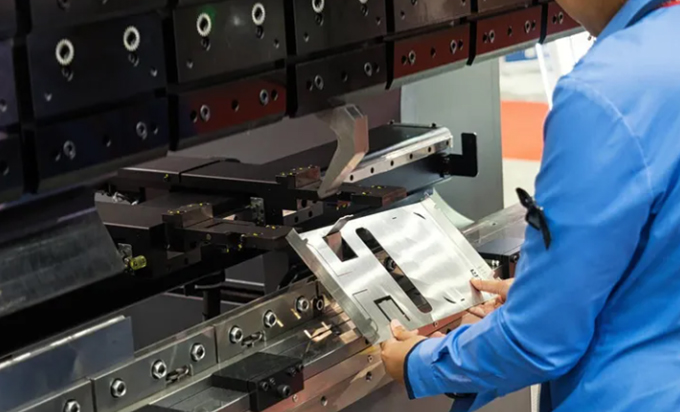
6.ダイカスト:
ダイカストは、溶融金属を高圧下で金型に注入して急速に凝固させ、目的の形状を形成するプロセスです。主な手順には、金型の準備、金属の溶解、射出、冷却、脱型が含まれます。
利点:
高精度: ダイカストでは、複雑な形状、複雑な詳細、正確な寸法の部品を製造できるため、一貫性と高精度が保証されます。
高い生産効率: ダイカストは大量生産に適しており、高速射出と急速冷却により高い生産率を実現します。
強度と耐久性: ダイカスト部品は通常、高い強度、剛性、耐食性などの優れた機械的特性を示します。
短所:
高コスト: ダイカストでは専用の金型の製造が必要であり、金型の製造および準備コストの点で高価になる可能性があります。
材料の選択が限られている: ダイカストは主に、アルミニウム合金、亜鉛合金、マグネシウム合金などの低融点金属に適用されます。鋼や銅などの高融点金属にはあまり適していません。
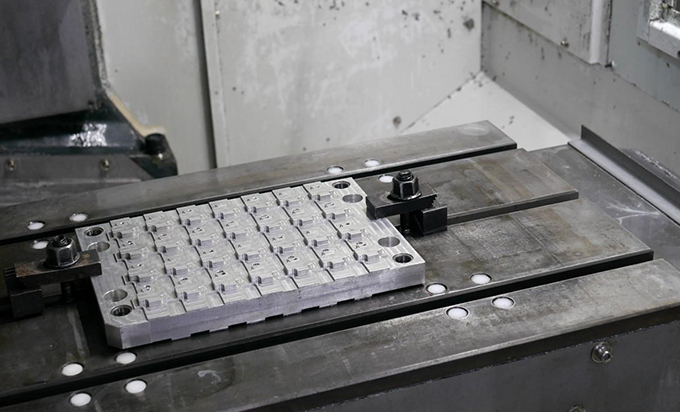
7.押し出し:
押出成形は、加熱した金属を押出機を使用して金型に押し込み、連続的な断面形状を形成するプロセスです。主な手順には、金属ビレットの予熱、押出、冷却、切断が含まれます。
利点:
効率的な生産: 押出成形は連続生産に適しており、長尺で大量の部品を迅速かつ効率的に製造できます。
多彩な形状: 押出成形により、中実、中空、複雑な形状などのさまざまな断面形状を製造でき、高い適応性を実現します。
材料の節約: 押出ダイの形状と寸法を制御することで、材料の無駄を最小限に抑えることができます。
短所:
精度に限界がある: ダイカストと比較して、押出成形は精度が低く、表面粗さが高くなります。
材料の制限: 押出成形は主にアルミニウムや銅などの展性のある金属に適しています。より硬い金属ではさらに困難になります。
金型の製造: 押出金型の製造とメンテナンスには専門的なスキルが必要であり、コストが高くなります。
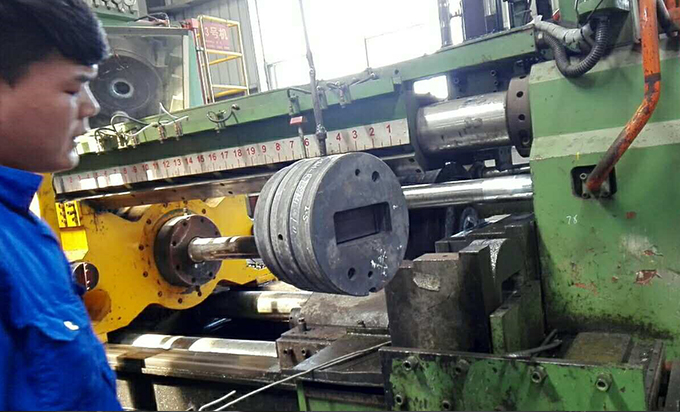
適切なカスタム金属加工方法を選択する方法
製品の設計と要件: 形状、寸法、材質、表面の要件など、製品の設計要件を理解します。さまざまな製品設計や要件に適した金属加工方法が異なります。
材料の選択:製品の特性と要件に基づいて、適切な金属材料を選択します。さまざまな金属材料がさまざまな加工方法に適しています。たとえば、アルミニウム合金は押出成形やダイカストに適しており、ステンレス鋼は CNC 加工や鋳造に適しています。
加工精度:製品の要求精度に応じて適切な加工方法を選択します。CNC 加工や研削などの一部の方法は、より高い精度と表面品質を提供できるため、高精度が要求される製品に適しています。
生産量と効率: 製品の生産量と効率の要件を考慮します。大規模な生産には、スタンピング、押出、ダイカストなどの高効率の加工方法が適している場合があります。小ロット生産やカスタマイズされた製品の場合、CNC 加工や 3D プリントなどの方法が柔軟性をもたらします。
コストの考慮事項: 設備投資、プロセス フロー、材料費など、加工方法のコスト要因を考慮します。加工方法が異なればコスト構造も異なるため、費用対効果を考慮する必要があります。
当社の専門エンジニアのチームは、幅広い金属加工方法に精通しており、貴重な洞察と推奨事項を提供できます。当社は業界の最新の進歩について深い知識を持っており、特定のプロジェクトに最適な方法を選択する際の複雑な問題を解決するお手伝いをいたします。
精密機械加工、鍛造、鋳造、その他の金属加工技術に関するサポートが必要な場合でも、当社のエンジニアがお客様の要件に合わせた指導を提供します。お客様が十分な情報に基づいた意思決定を行えるよう、材料特性、必要な公差、生産量、コストの考慮事項などの要素を考慮します。
さらに、当社のエンジニアは、製造可能性を考慮して金属コンポーネントの設計を最適化するサポートを提供し、選択した加工方法を使用して効率的に製造できるようにします。製品の全体的な品質、機能性、費用対効果を向上させるための設計変更のご提案をいたします。
お気軽にお問い合わせください。金属加工で最高の結果が得られるようお手伝いいたします。
投稿日時: 2023 年 12 月 18 日