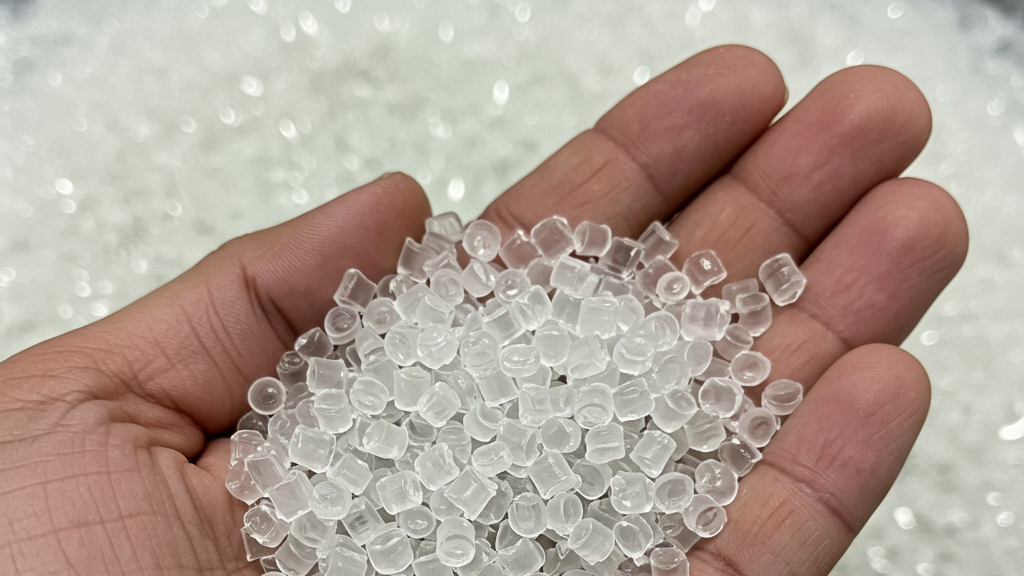
The selection of materials for food contact injection molded components is crucial, directly impacting product safety and durability. Polycarbonate (PC) and Thermoplastic Polyurethane (TPU) are two commonly used high-performance plastics, each offering distinct advantages in food contact applications.
After understanding the basic properties of PC and TPU, it is essential to consider the stringent standards for food contact materials. We will analyze the performance of PC and TPU in these aspects and explore their suitability for different food contact applications.
What are the advantages and disadvantages of PC and TPU in food applications?
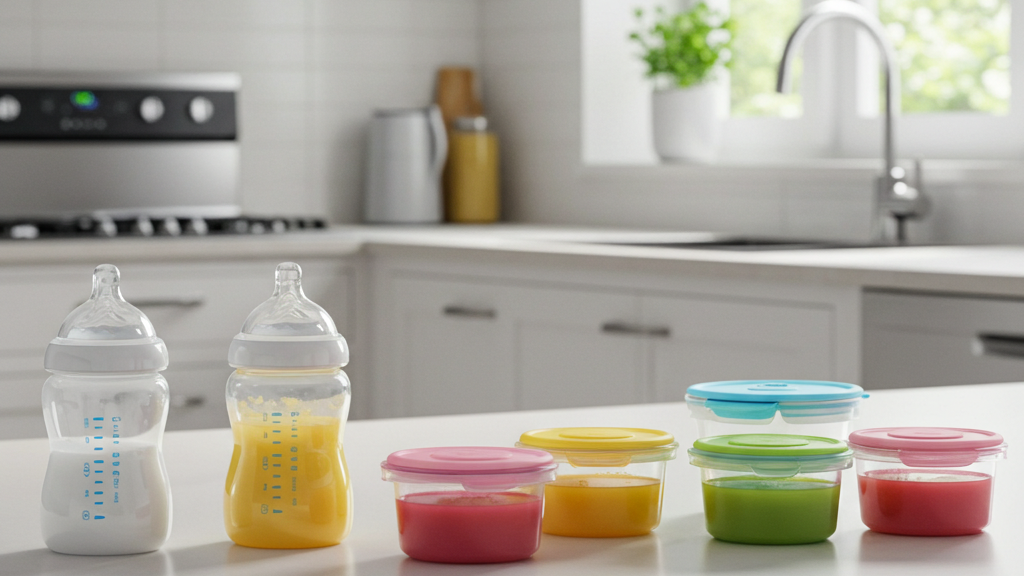
Material selection is directly related to the safety and functionality of the product. PC and TPU, as two commonly used high-performance plastics, exhibit unique advantages and disadvantages in applications. Understanding these characteristics is crucial for optimizing product design.
- Strength vs. Transparency: PC offers high strength and transparency, but its chemical resistance and susceptibility to scratches are its main drawbacks in food applications.
- Flexibility and Wear Resistance: TPU is renowned for its excellent flexibility and wear resistance, but it has relatively low heat resistance, and hardness selection must be carefully considered.
- Material Selection: In food applications, the key to choosing between PC and TPU lies in balancing the physical properties of the materials with food safety requirements.
- Food Safety: Whether using PC or TPU, selecting materials that comply with food safety standards is a prerequisite for ensuring the safety of food contact products.
What Safety Standards Must Food Materials Meet?
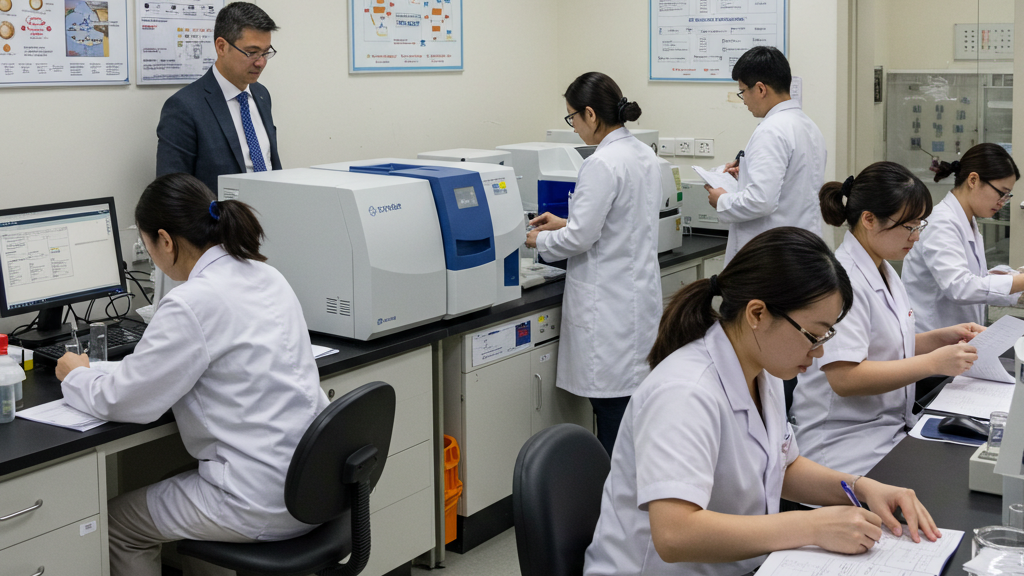
From raw material selection to the final product, the safety of food contact materials must be ensured throughout the entire production process. Strict safety standards are not only a responsibility to consumers but also a cornerstone of sustainable development for enterprises.
- Specific Material Requirements: Different materials must comply with their respective national standards, with strict control over the content and migration of specific harmful substances.
- International Standards:In addition to national standards, food contact materials may also need to meet international standards such as those in the EU and the US to ensure global safety.
- Labeling and Traceability: Clear labeling and perfect traceability systems are key to safeguarding consumers’ right to information and the efficiency of product recalls.
- Continuous Updates: Food safety standards are continuously updated, and enterprises must stay informed and ensure their products comply with the latest requirements.
How to Choose the Right PC or TPU Material Based on Specific Needs?
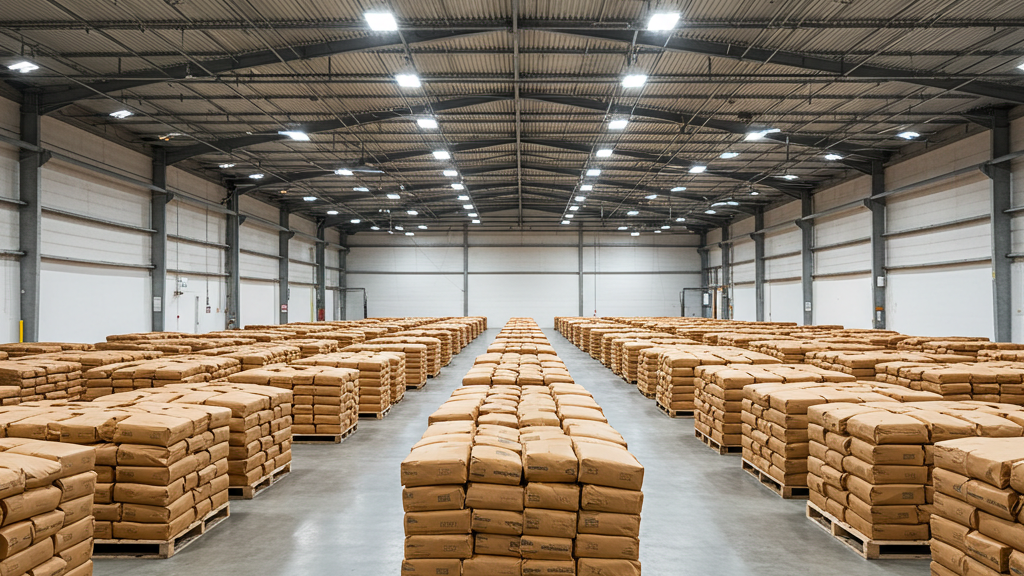
In food contact applications, PC and TPU each have their unique advantages, but the choice between them is not universal. Only by thoroughly understanding the specific application requirements can the best choice be made to ensure product safety and functionality.
- Product Intended Use: Based on the functional needs of the product, such as strength, flexibility, transparency, and abrasion resistance, choose the most suitable material.
- Operating Environment: Consider the product’s operating temperature, chemical exposure, and outdoor conditions to ensure the material can withstand the expected environmental factors.
- Food Safety Standards: Strictly adhere to relevant food contact material safety standards to ensure the selected material’s migration properties and composition meet the requirements.
- Cost Considerations: While meeting functional and safety requirements, comprehensively evaluate material and processing costs to choose an economically viable solution.
Application considerations of PC and TPU
Consideration Factors |
PC (Polycarbonate) |
TPU (Thermoplastic Polyurethane) |
Product Intended Use | ||
Rigidity & Strength | High strength, rigidity, suitable for food containers, tableware, etc. | Flexibility, elasticity, suitable for seals, hoses, flexible packaging, etc. |
Transparency | High transparency, suitable for containers or packaging requiring visibility of food contents | Relatively lower transparency, but some TPUs have good transparency |
Abrasion Resistance | Relatively poor, prone to scratches | Excellent, suitable for food processing equipment parts, etc. |
Usage Environment | ||
Temperature Range | High heat resistance, suitable for high-temperature sterilization, hot filling, etc. | Lower heat resistance, avoid long-term use in high-temperature environments |
Chemical Contact | Sensitive to some chemicals, consider food acidity, oil content, etc. | Good chemical resistance, but consider the resistance of specific chemicals |
Outdoor Use | UV resistance needs consideration, prone to aging | UV resistance needs consideration, some TPUs have good weather resistance |
Food Safety Standards | ||
Migration | Must comply with GB 4806 standards, focus on specific harmful substance migration | Must comply with GB 4806 standards, focus on specific harmful substance migration |
Composition | Choose food-grade PC materials | Choose food-grade TPU materials |
Cost Considerations | ||
Material Cost | Higher | Higher, some grades are even more costly |
Processing Cost | Varies depending on specific processes | Varies depending on specific processes |
Development Trends of Food Contact Injection Molding Materials
The development trends of food contact injection molding materials are being driven by multiple factors, including increasing consumer focus on sustainability, stringent safety requirements from regulatory bodies, and technological innovations.
1.Sustainability: Bio-based and biodegradable materials will become mainstream to reduce environmental impact.
2.Recycling: Advancements in recycling and circular economy technologies will promote the use of recycled plastics in food contact applications.
3.Enhanced Performance: Advanced technologies such as nanocomposites and coatings will significantly improve the barrier properties of materials.
4.Smart Solutions: Smart packaging technologies, including sensors and indicators, will enhance food safety and reduce waste.
Conclusion
The future of food contact injection molding materials will be driven by sustainability, recycling, enhanced performance, smart technologies, and stringent food safety standards.
For expert assistance in implementing for your production needs, visit our resource center or contact us. Let’s help you scale up your manufacturing with precision and efficiency!
Post time: Mar-20-2025