The specifications and information of current products have become an indispensable part. Most manufacturers will engrave the information on the products through silk screen printing, pad printing or metal engraving. However, do you really understand the advantages and disadvantages and differences of each engraving method? Today, this article will focus on the advantages and disadvantages, printing speed, and difficulty to introduce the differences between metal engraving and pad printing.
Advantages and disadvantages of Pad printing
Pad printing, as a printing technology, has many advantages in modern manufacturing, making it widely used in various fields. Compared with laser marking, pad printing technology has some major advantages:
1.Strong adaptability: Pad printing is suitable for a variety of materials, including plastic, rubber, metal, glass, etc., so it is widely used in many industries such as electronic manufacturing, toy production, and decoration manufacturing.
2.No surface damage: During the pad printing process, no direct physical or chemical changes will occur on the surface of the material. Conversely, laser marking may cause minor surface changes in some materials.
3.Various colors: Pad printing uses ink for printing, which can achieve a variety of colors and effects, including transparent, glossy, matte, etc. This opens up more possibilities for pad printing in terms of decoration and identification.
4.Low cost: Pad printing setup costs are quite low, and the pad printing equipment does not take up much space. Pad printing generally has lower manufacturing costs than some high-precision printing technologies.
5.Production speed: For some mass production situations, pad printing can print a large number of products in a shorter time because it does not require the fine focus of the laser beam like laser marking.
6.Various printing effects: pad printing can realize complex patterns, logos, text, etc., with high decorativeness and personalized customization capabilities.
7.Coping with Irregular Surfaces: Pad printing technology can be used on objects of different shapes and unevenness. In contrast, laser marking may require more adjustments and adaptation to complex shapes.
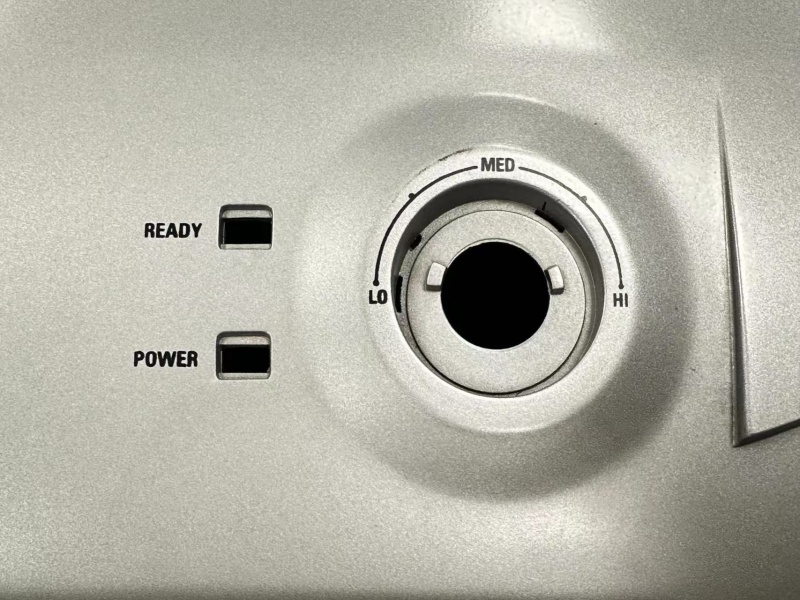
As a surface printing technology, pad printing has many advantages, but also has some disadvantages and limitations. Here are some of the main disadvantages of pad printing technology:
1.Limited Accuracy: Pad printing technology is limited in the accuracy of patterns and text. Due to the elasticity of the printed tape and the manufacturing process, the details of the pattern may not be as detailed as with laser marking technology.
2.Lack of durability: Compared to laser marking technology, its durability may be lower. Prolonged exposure to the outside environment may cause fading, wear or peeling.
3.Preparation and replacement of printing tape: Pad printing requires special printing tape, and only one color of ink can be printed at a time when using pad printing. Therefore, when printing different patterns on different materials, it takes a certain amount of time and resources to replace the printing tape.
4.Relatively low productivity: Compared with some laser markings, pad printing has relatively low productivity. Each printing process takes a certain amount of time, which can be a limiting factor in mass production.
5.Hazardous waste disposal: Waste generated during the pad printing process, including waste printing tape and waste ink that may contain harmful substances. The disposal of these wastes may require special environmental protection measures.
Advantages and disadvantages Mater Engraving
Compared with pad printing technology, laser marking technology has obvious advantages in terms of accuracy, durability, scope of application, and flexibility. The following are the main advantages of laser marking technology compared with pad printing technology:
1.High precision and clarity: The focused nature of the laser beam allows for the creation of sharper patterns on the surface of the material, suitable for applications requiring high-precision marking.
2.High durability: Marks produced by laser marking are usually extremely durable. Because the laser beam directly causes changes in the chemical or physical properties of the material surface, the marking is not easy to fade, peel off, or be affected by the external environment.
3.Wide range of applications: Laser marking technology is suitable for many types of materials, including metals, plastics, glass, ceramics, etc. Its flexibility makes it applicable to a wider range of fields.
4.Non-contact processing: Laser marking is a non-contact processing technology. The laser beam is directly irradiated on the surface of the material without any physical contact, so it will not damage the surface of the material.
4.Fast and efficient: Since the laser beam travels at the speed of light, it can complete the marking in an instant, suitable for scenarios that require high-efficiency production.
5.No waste generation: Laser marking is a waste-free technology as it does not require printing tape or ink, thus reducing the problem of waste disposal.
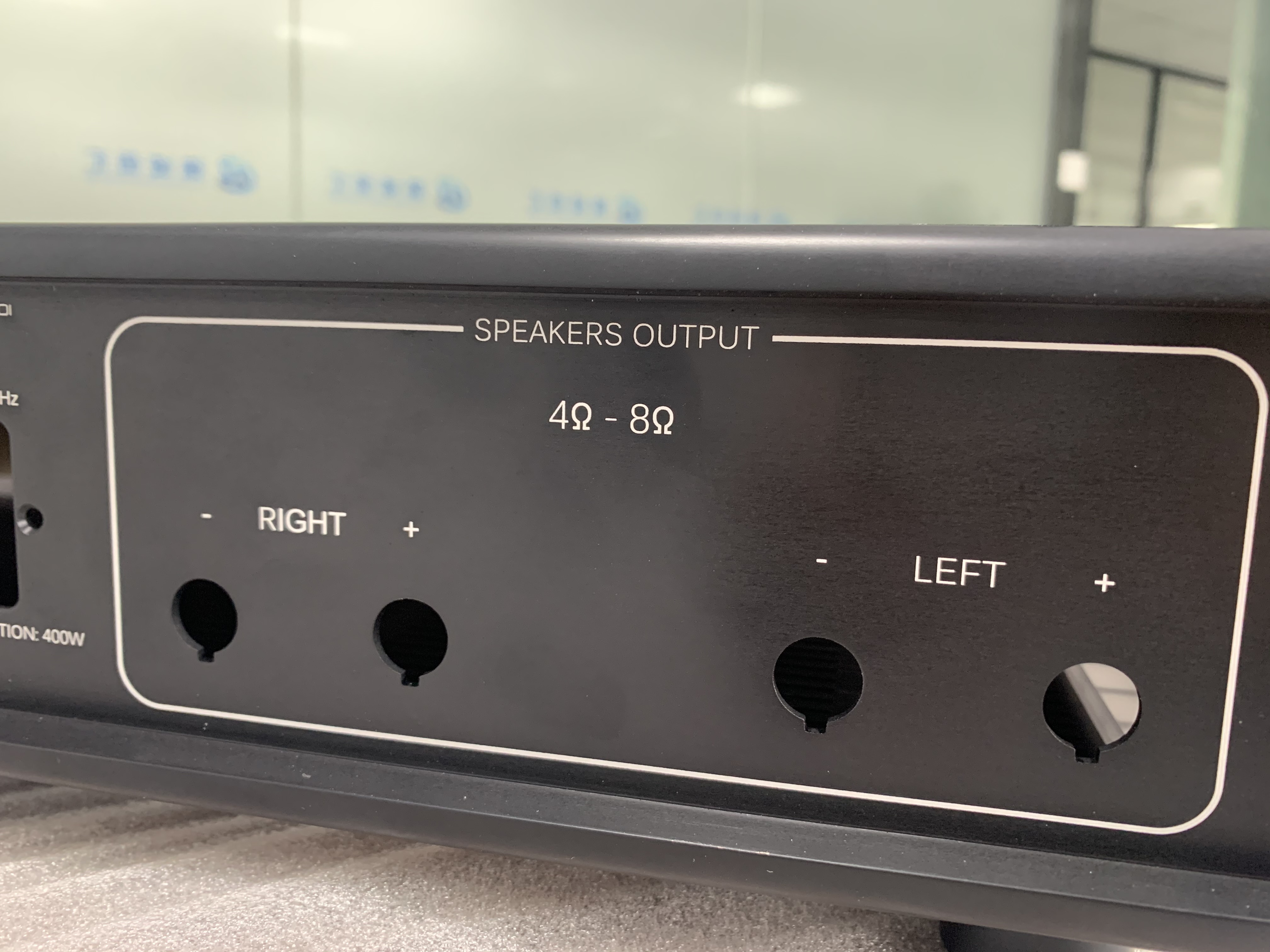
Compared with pad printing technology, laser marking technology also has some disadvantages. Here are some of the main disadvantages of laser marking technology compared to pad printing:
1.Higher equipment costs: Laser marking equipment typically has higher purchase and maintenance costs, which increases the initial investment.
2.Complex debugging and operation: Laser marking technology requires precise adjustment of laser parameters to achieve ideal marking results. This may require some technical knowledge and training on the part of the operator.
3.Safety issues: Laser beams have high energy and may cause harm to operators if not handled properly. Therefore, operators need to follow strict safety operating procedures.
4.Limited applicability: While laser marking technology is suitable for many materials, it is not suitable for all materials. Certain high temperature, highly reflective or highly absorbent materials may not be suitable for laser marking.
5.Limitations on complex shapes: Although laser marking technology is flexible, it can be limited when dealing with certain complex-shaped objects, especially those with uneven surfaces or concave-convex structures.
Different
Mater engraving |
Pad printing |
|
Light-transmitting |
Yes |
No |
Color |
Consistent with the material |
Consistent with pigment |
Abrasion resistance |
Strong |
Weak |
Principle |
Photo lithography |
Physical adhesion |
Aesthetics |
Low |
High |
Environmental protection |
High |
Low |
Difficulty |
Simple |
Difficult |
1. The pattern or nameplate produced by metal engraving has strong light transmittance because it adopts the principle of photo etching. Both pad printing and silk screen printing transfer the pigment to the product itself, so the pattern drawn has poor light transmittance.
2. Silk screen printing and pad printing mainly transfer ink to the product to produce specific patterns. Compared with engraving, the pattern design process directly on the product itself, the patterns produced by silk screen printing and pad printing are more easily worn.
3. Both processes will have slight pollution. The pollution of silk screen printing lies in the evaporation of ink in the later stage of the finished product, while metal engraving will produce subtle harmful gases during the engraving process. But in fact, it will not cause serious harm to the human body.
4. Compared with the complex process of pad printing, metal engraving directly inputs the pattern or information required by the customer into the computer and then directly engraves it through the machine. Therefore, metal engraving has a natural advantage in terms of difficulty. It is also consistent in printing speed.
5.The minimum line width of the UV laser lettering machine produced can reach 0.01mm, which is much more accurate than that of silk screen printing.
6.The price of screen printing is cheaper than that of laser lettering machine, but in the later period, it is often necessary to buy consumables such as ink, but there are almost no consumables for laser lettering machine after purchase.
7.Consider the type of material you are dealing with. Pad printing is suitable for a variety of materials, including flexible materials, while laser marking is adaptable to a wide range of materials.
Summary
To sum up, as different material surface processing technologies, pad printing and laser marking have obvious differences in principle, process flow, and applicable fields. According to different application requirements, manufacturers can choose suitable processing technology to achieve the best processing effect and durability.
To learn more about laser marking solutions, contact us today or request a quote.
Post time: Jun-11-2024