プラスチックめっきは、エレクトロニクス産業、防衛研究、家電製品、日用品などで広く使用されているめっきプロセスです。プラスチックめっきプロセスの適用により、金属材料の使用量が大幅に節約され、金属材料に比べて加工工程が簡単で自重も軽いため、プラスチックめっきプロセスを使用して製造される機器も軽量化され、装置の軽量化も可能になります。機械的強度が高く、より美しく耐久性のあるプラスチック部品の外観。
プラスチックメッキの品質は非常に重要です。プラスチックめっきの品質に影響を与える要因には、めっきプロセス、操作、プラスチック加工など多くの要因があり、プラスチックめっきの品質に大きな影響を与える可能性があります。
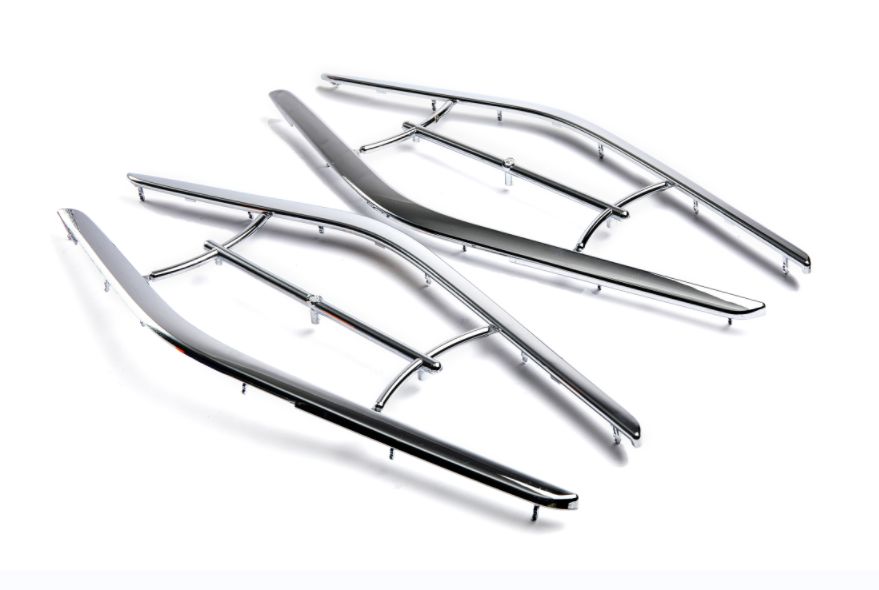
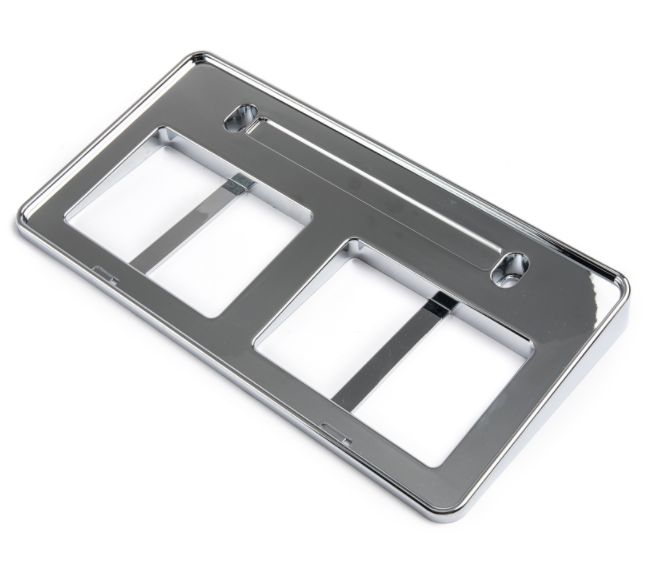
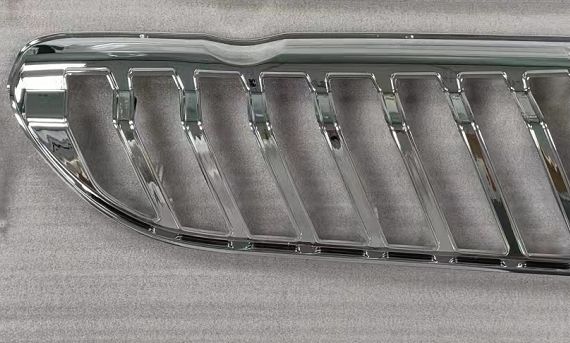
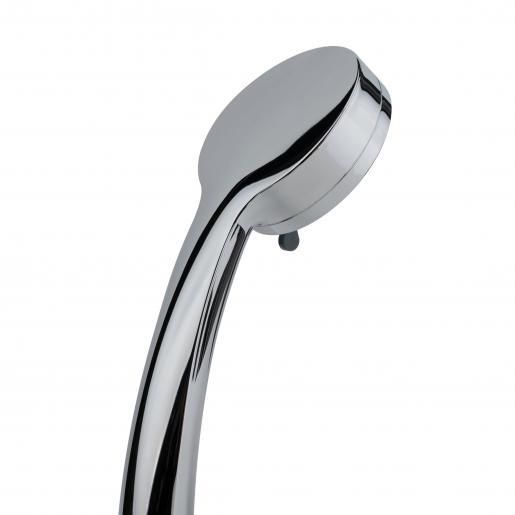
1. 原材料の選択
市場にはさまざまな種類のプラスチックがありますが、それぞれのプラスチックに独自の特性があるため、すべてにめっきできるわけではありません。また、めっきを行う際には、プラスチックと金属層の結合や物理的性質の類似性を考慮する必要があります。プラスチックと金属のコーティング。現在メッキ可能なプラスチックはABSとPPです。
2.部品の形状
A)。プラスチック部品の収縮を引き起こす不均一を避けるために、プラスチック部品の厚さは均一である必要があります。めっきが完了すると、その金属光沢は同時により明確な収縮を引き起こします。
また、樹脂部品の肉厚が薄すぎるとメッキ時に変形しやすくなり、メッキの密着が悪くなったり、使用中に剛性が低下してメッキが剥がれやすくなります。
B)。ブラインドホールは避けてください。ブラインドソレノイドに残った処理液は簡単に洗浄できず、次の工程で汚染を引き起こし、めっきの品質に影響を与えます。
C)。めっきのエッジが鋭利な場合は、めっきの作業がより困難になります。鋭利なエッジは発電の原因になるだけでなく、めっきの角が膨らむ原因にもなります。そのため、丸みを帯びたコーナー移行部を選択するようにしてください。少なくとも0.3mm以上。
平らなプラスチック部品にメッキを施す場合、平らな形状だとメッキの際に中央が薄く端が厚いメッキムラができてしまいますので、平面を少し丸く加工するか、マットな表面にしてメッキするようにしてください。また、めっきの光沢の均一性を高めるために、めっき表面積の大きいプラスチック部品をやや放物線状になるように設計してください。
D)。メッキや突起が焦げやすい場合、深い凹みがあるとプラスチックが露出する傾向があるため、プラスチック部品の凹みや突起を最小限に抑えます。溝の深さは溝の幅の1/3を超えてはならず、底は丸みを帯びている必要があります。グリルがある場合は、穴の幅は梁の幅と等しく、厚さの1/2以下にしてください。
E)。メッキ部は十分な取付位置を設計し、吊り具との接触面は金属部の2~3倍程度としてください。
F)。プラスチック部品は金型内でめっきし、めっき後に離型する必要があるため、脱型中にめっき部品の表面を操作したり、無理に力を入れてめっきの結合に影響を与えたりしないように、プラスチック部品の離型が容易になるように設計する必要があります。 。
G)。ローレット加工が必要な場合、ローレット加工の方向は離型方向と同じで直線になるようにしてください。ローレット縞と縞の間の距離はできるだけ大きくする必要があります。
H)。インレーが必要なプラスチック部品の場合、メッキ前の処理により腐食性が生じるため、金属インレーの使用はできるだけ避けてください。
私)。プラスチック部品の表面が平滑すぎると、めっき層の形成に寄与しないため、二次プラスチック部品の表面はある程度の表面粗さを有する必要があります。
3.金型設計・製作
A)。金型の材質はベリリウム青銅合金ではなく、高品質の真空鋳鋼を使用してください。キャビティの表面は、金型の方向に沿って凹凸が 0.21μm 未満になるまで鏡面研磨し、ハードクロムメッキを施すことが望ましいです。
B)。プラスチック部品の表面は金型キャビティの表面を反映するため、電気メッキされたプラスチック部品の金型キャビティは非常にきれいである必要があり、金型キャビティの表面粗さは、金型キャビティの表面の表面粗さよりも 12 グレード高くなければなりません。一部。
C)。パーティング面、フュージョンライン、コアインレイラインはめっき面上に設計しないでください。
D)。ゲートは成形品の最も厚い部分に設計する必要があります。キャビティを充填するときに溶融物が急速に冷却されないようにするには、ゲートをできるだけ大きくする必要があります (通常の射出成形金型より約 10% 大きい)。できればゲートとスプルーの断面は円形で、長さはスプルーは短くする必要があります。
E)。空気フィラメントや部品表面の気泡などの欠陥を避けるために、排気穴を設ける必要があります。
F)。エジェクタ機構は、金型から部品をスムーズに取り出せるように選択する必要があります。
4.プラスチック部品の射出成形工程の条件
射出成形プロセスの特性上、内部応力の発生は避けられませんが、プロセス条件を適切に制御することで内部応力が最小限に抑えられ、部品の正常な使用が保証されます。
以下の要因はプロセス条件の内部応力に影響を与えます。
A)。原料の乾燥
射出成形工程において、めっき部品の原料が十分に乾燥していない場合、部品表面に空気フィラメントや気泡が発生しやすくなり、皮膜の外観や接合力に影響を与えます。
B)。金型温度
金型の温度はめっき層の結合力に直接影響します。金型温度が高いと樹脂の流れが良くなり、部品の残留応力が小さくなり、めっき層の密着力が向上します。金型の温度が低すぎると、中間層が 2 層形成されやすくなり、めっき時に金属が析出しなくなります。
C)。処理温度
加工温度が高すぎると、不均一な収縮が発生して体積温度応力が増加し、シール圧力も上昇するため、スムーズな離型には冷却時間が長くなります。したがって、処理温度は低すぎても高すぎてもいけません。プラスチックの流動を防ぐために、ノズル温度はバレルの最高温度よりも低くする必要があります。冷たい材料が金型キャビティに流入するのを防ぎ、塊、石、その他の欠陥の生成とメッキ不良の原因を回避します。
D)。射出速度、射出時間、圧力
この 3 つを十分に習得していないと残留応力の増加を引き起こすため、射出速度を遅くし、射出時間をできるだけ短くし、射出圧力を高すぎないようにすることで、残留応力を効果的に低減できます。ストレス。
E)。冷却時間
冷却時間は、金型が開く前に金型キャビティ内の残留応力が非常に低いレベルまたはゼロに近づくように制御する必要があります。冷却時間が短すぎると、強制的な離型により部品に大きな内部応力が発生します。ただし、冷却時間を長くしすぎないでください。長くしないと、生産効率が低くなるだけでなく、冷却収縮によって部品の内層と外層の間に引張応力が発生します。これらの極端な両方により、プラスチック部品上のメッキの結合が減少します。
F)。離型剤の影響
メッキされたプラスチック部品には離型剤を使用しないのが最善です。油性離型剤は、プラスチック部品の表層に化学変化を引き起こし、その化学的特性を変化させ、めっきの接着不良を引き起こす可能性があるため、使用できません。
離型剤を使用する必要がある場合は、型を離すためにタルカム パウダーまたは石鹸水のみを使用してください。
めっきプロセスにおける影響要因が異なるため、プラスチック部品はさまざまな程度の内部応力にさらされ、それがめっきの結合力の低下につながり、めっきの結合力を高めるための効果的な後処理が必要になります。
現在、熱処理と表面仕上げ剤による処理の使用は、プラスチック部品の内部応力の除去に非常に優れた効果をもたらしています。
また、めっき部品の梱包・検査には細心の注意が必要で、めっき部品の外観を損なわないよう特別な梱包を行う必要があります。
Xiamen Ruicheng Industrial Design Co.、Ltdはプラスチックメッキに関する豊富な経験があります。ご必要な場合はお気軽にお問い合わせください。
投稿日時: 2023 年 2 月 22 日